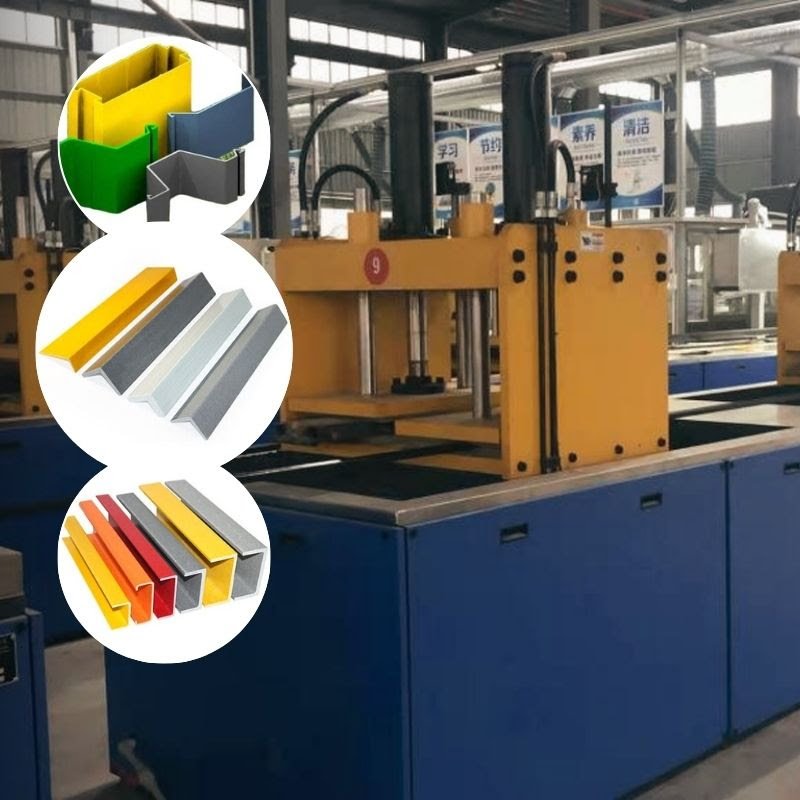
Pultrusion machines are essential in producing high-strength composite materials, especially in industries that require sturdy, durable products like construction, automotive, and aerospace. As demand for composite materials grows, maximizing production efficiency with pultrusion machine is crucial for maintaining profitability and meeting client needs. Here, we’ll explore tips for optimizing performance and ensuring consistent maintenance to keep your pultrusion machine running smoothly.
Understanding the Pultrusion Machine Process
A pultrusion machine is designed to continuously pull materials through a die to shape them into strong, lightweight profiles. The process begins with fiber reinforcements, typically glass or carbon, which are pulled through a resin bath to create a composite material. This material then goes through a heated die, curing and hardening to form its final shape. Pultrusion machines offer continuous production and high efficiency, making them ideal for high-volume manufacturing.
1. Optimize Machine Settings for Maximum Efficiency
Properly adjusting the machine settings can make a significant difference in production output. Here’s what to consider:
- Speed Control: Find the optimal pulling speed that doesn’t compromise the material’s strength. Faster speeds may increase production but can lead to defects if the material doesn’t have time to cure properly.
- Temperature Settings: Make sure the die temperature is suitable for the resin type. If it’s too high, the material may degrade; too low, and it may not cure completely.
- Resin Ratios: Adjust the resin-to-reinforcement ratio as needed. The right balance ensures product quality and durability, so make sure this setting aligns with the specifications of the final product.
2. Maintain a Clean and Consistent Workspace
A clean workspace is crucial for any manufacturing process but is especially important for pultrusion. Here’s how to maintain cleanliness:
- Dust and Particle Control: Dust and other particles can interfere with the resin and fibers, causing imperfections. Regularly clean the area around the pultrusion machine to reduce contaminants.
- Resin and Fiber Storage: Store resin and fiber materials in a controlled environment to prevent contamination. Make sure that materials are kept dry and clean before use.
3. Regular Maintenance of the Pultrusion Machine
Preventative maintenance keeps your pultrusion machine in top shape, reducing the risk of downtime. Key maintenance tasks include:
- Inspecting and Replacing Wear Parts: Components like dies, pulling mechanisms, and rollers are prone to wear over time. Regularly inspect and replace these parts to maintain smooth operation.
- Lubrication: Proper lubrication of moving parts reduces friction, preventing breakdowns and extending the lifespan of your machine.
- Electrical Systems Check: Inspect the electrical components of the pultrusion machine regularly to ensure all systems are functioning properly, and replace any worn-out wiring to prevent electrical issues.
4. Training Operators for Skill and Efficiency
Well-trained operators are essential for maximizing production with a pultrusion machine. Here are training focus areas:
- Machine Operation: Ensure operators understand how to adjust settings, identify issues, and respond quickly to changes in the production process.
- Quality Control: Train operators to inspect finished products for quality, identifying defects like surface irregularities or improper curing before they reach the end of the line.
- Safety Protocols: Safety is paramount when working with heavy machinery and chemicals. Training should cover proper handling of materials, safe machine operation, and emergency procedures.
5. Invest in Quality Materials
Quality in equals quality out. High-grade resin and fiber reinforcements are critical for producing reliable composite products. Substandard materials may lead to defective products, increased waste, and higher maintenance needs. Although quality materials may come at a higher cost, the long-term savings in reduced rework and extended machine life make it a wise investment.
6. Monitor Production and Adjust as Needed
Consistently monitoring production allows for adjustments before small issues turn into big problems. Here’s what to keep an eye on:
- Output Quality: Regular quality checks ensure that products meet specifications. Track dimensions, strength, and finish for consistency.
- Machine Performance Metrics: Monitoring metrics like machine uptime, cycle times, and energy consumption can provide insights into areas for improvement.
- Feedback Loop: Encourage feedback from operators on potential improvements or recurring issues. Often, those working directly with the machine can spot areas that may benefit from adjustment.
7. Upgrade When Necessary
As with any technology, advancements in pultrusion machines continue to improve production efficiency. While regular maintenance can extend the life of a machine, upgrading to a newer model may offer significant benefits, including faster production speeds, enhanced precision, and improved energy efficiency. Evaluate the costs and benefits of upgrading versus maintaining an older model to determine the best option for your production needs.
8. Implement an Effective Maintenance Schedule
A structured maintenance schedule ensures that your pultrusion machine receives regular attention, preventing unexpected downtime. This schedule should include:
- Daily Checks: Quick inspections of machine components, lubrication levels, and workspace cleanliness.
- Weekly Inspections: A more thorough inspection of wear parts, pulling mechanisms, and temperature controls.
- Monthly or Quarterly Maintenance: Deep cleaning, part replacements, and any calibration or alignment necessary for optimal machine performance.
The Benefits of Proper Maintenance and Optimization
Keeping a pultrusion machine in top condition through maintenance and optimized settings has numerous benefits:
- Increased Production Output: By reducing downtime and defects, you can maximize production rates.
- Consistent Quality: Proper machine maintenance and optimized settings ensure that each product meets quality standards.
- Lower Costs: Fewer defects and breakdowns mean lower repair and rework costs.
- Extended Machine Life: Regular maintenance extends the life of the machine, giving you a greater return on investment.
Conclusion
By focusing on optimizing machine settings, maintaining cleanliness, training skilled operators, and implementing regular maintenance, manufacturers can maximize the productivity of their pultrusion machines. Investing time and resources into these practices not only boosts production but also ensures long-term profitability and equipment longevity. Remember, a well-maintained pultrusion machine is the key to reliable, efficient, and high-quality production.